Attention Span Can Affect Safety Performance
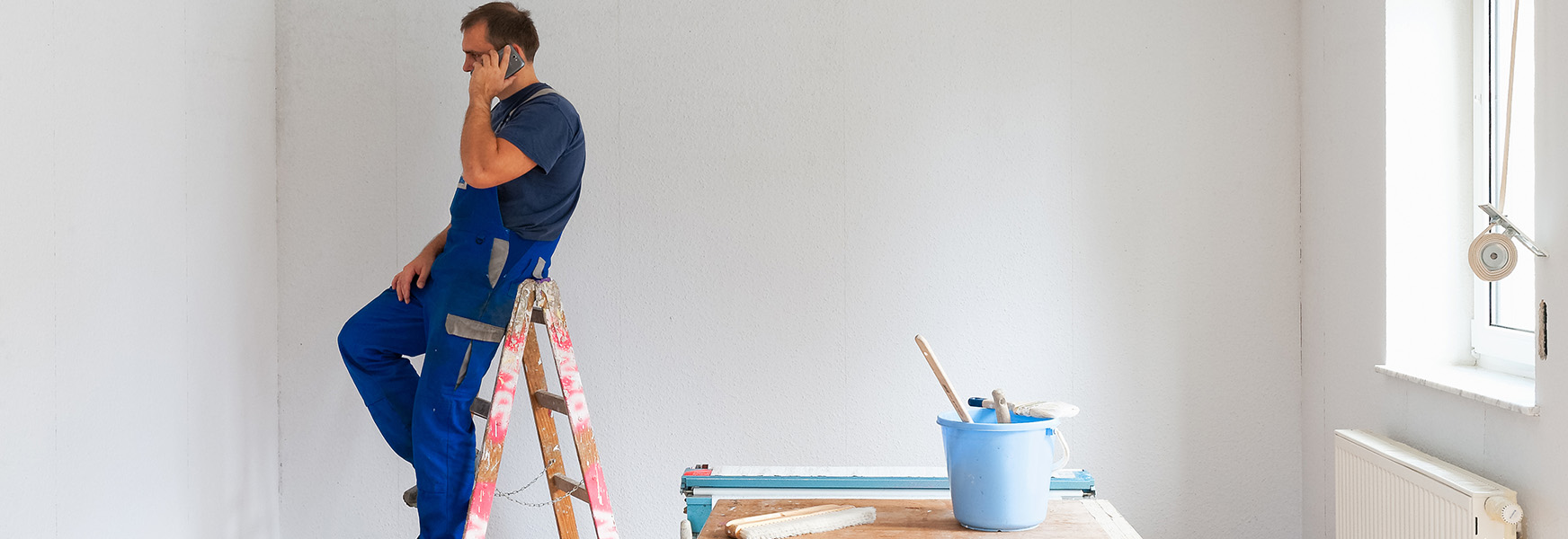
What do you think of when you read or hear this phrase? Some of us may recall how rapper and music producer Eminem kicked off one of his most iconic raps with it (“May I have your attention please? May I have your attention please?”). Others may think of television personality James Corden’s self-titled book. How about being at a large event as part of the crowd? To me, it sounds like something an event host would say. Well, whether you notice it or not, something or someone is constantly vying for our attention.
Why all this attention to… attention? It seems attention, or the lack thereof, is likely a contributing factor to many unsafe behaviors and incidents, despite all the hours devoted to safety training.
Our work environments often feature many moving pieces, equipment, and people that can make it challenging to remain engaged or fully present and focused on the primary task at hand. Our recognition of hazards and safety performance can suffer when distracted. We know awareness plays a significant role in slip, trip and fall events – a frequency and severity loss leader for just about every business. Understanding relevant cues and selecting appropriate actions can also suffer when our capacity to pay attention runs low due to competing demands or distractions. Digital distractions have reportedly increased the risk of accidents and affected product quality, customer service, and quality of care.
Depending on the type of human error or mistake committed, training and constructive feedback can be helpful strategies to avoid future mishaps. This is the case when there are clear rules to follow. But at some point, everyone makes mistakes … even those who are well-trained, motivated, and experienced. Leaders who expect and prepare for the inevitable mistake tend to look at how and why all the controls in place did not prevent it (i.e., systems-based approach), rather than simply blaming the person(s) involved.
To help keep one’s attention on point, start with identifying the causes of inattention, distractions, or interruptions. A plan of action can then be developed. A piece of this should involve staff education on why maintaining attention is so vital and what can happen when it is not. Discussing common examples (e.g., talking to someone while prepping food with a knife), as well as those less typical, should be included. Individual check-in questions (see below) can be developed, and practice expectations set.
Individual Check-in Questions
Recognize:
- What is expected of me and others in this situation?
- Am I actively engaged or fully present?
- What hazards are present; how could I get injured?
- What is different or familiar about this situation?
Understand:
- What cues are more relevant to the situation?
- Do I need more information (context, prior task, goals)?
- Do I have what I need to act safely?
- Should I pause?
- What could go wrong?
Act:
- What lessons did I learn?
- What do I need to consider next time?
- What changes should I make?
Checklists or other means to document and track progress within a task have been suggested. No talking or interruption areas, zones, or times have been implemented. Headphones or earbuds are commonly not allowed when operating or working near heavy equipment. Signs have been used to communicate these rules to employees and the public.
Team members and team performance can benefit from frequent communications that are clear, concise, complete, and constructive. Situations should be practiced by teams to better understand the effects of personal filters or biases in recognizing hazards and understanding situations.
I hope I got your attention! Think about where attention or inattention has been cited as a contributing factor or cause of past incidents. Think about whether retraining of known rules has supported better attention. If not, consider paying closer attention to the ideas covered, contact your Safety Management Consultant, or submit a question to Ask A Safety Expert.