Safety Inspections - The Hard and the Soft
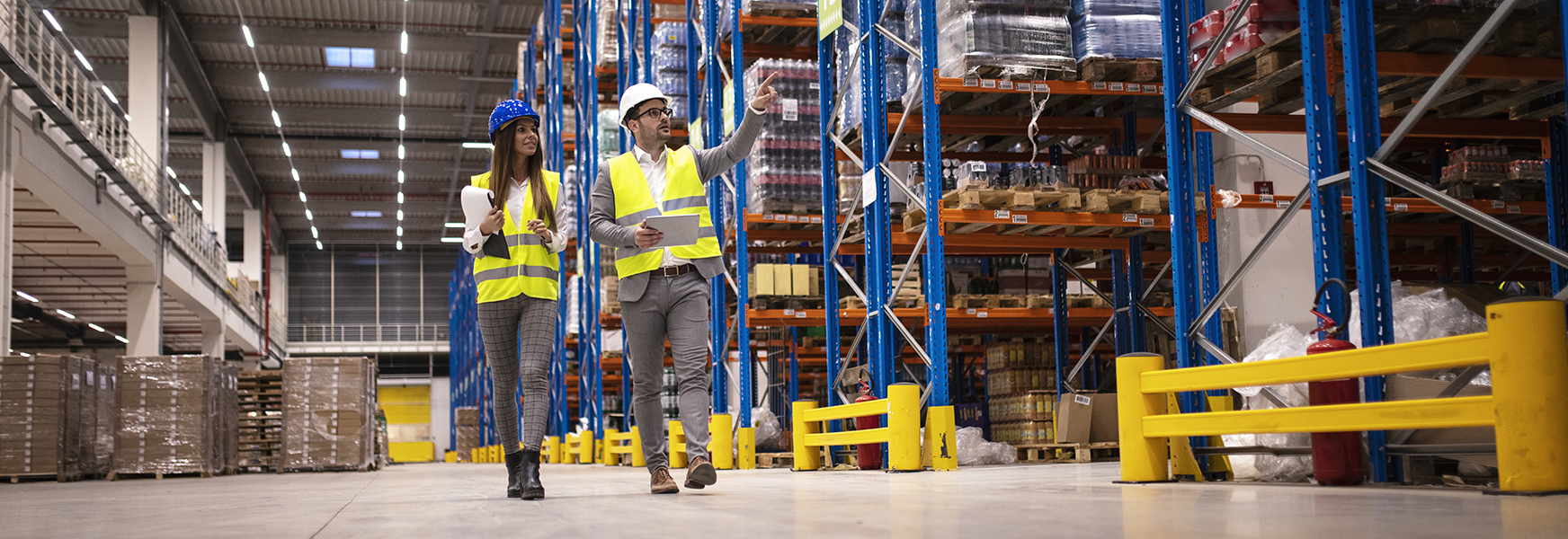
We all know the importance of conducting regularly scheduled site inspections as part of any comprehensive safety program. But there are two distinct approaches to these inspections that will often yield different results that are both helpful to workplace safety improvement. Over the years, I’ve come to identify these two inspection types as the hard science and soft science.
The “hard” science are the specific and measurable hazards and controls as outlined in policies, procedures, and safety and health regulations. For example, specific OSHA standards which define how high, how far, how many, and how something is to be constructed. This might involve using a “gotcha stick” to accurately measure barrier openings, or a tape measure to determine guardrail heights or exit widths. It might also mean determining exposure limits like threshold limit values (TLV) or ensuring fire extinguishers are accessible and inspected monthly. Obviously, this list goes on and on. This is an important exercise as we take our checklists and determine if things are measuring up, then we record for documentation and corrective action.
The “soft” science is a more intangible part of the inspection process. This involves looking at the human side of the working area and operating procedures. According to Dictionary.com, “soft science” is defined as, “any of the specialized fields or disciplines, as psychology, sociology, anthropology, or political science, that interpret human behavior, institutions, society, etc., on the basis of scientific investigations for which it may be difficult to establish strictly measurable criteria.” That’s a mouthful, but it does relate directly to safety inspections. Essentially, we observe to ensure employees appear fully engaged in the safety process. We can even get clues through their non-verbal communication. I have been through jobsites where the employees make eye contact and fully engage with everyone and everything. Conversely, I have also been at jobsites where workers make no eye contact and only grudgingly give answers to questions. The climate is negative, housekeeping is haphazard, and although the measurable safety items are in compliance, the mood is uncomfortable. These observations are not on the typical inspection form, but tells you a lot about the jobsite, the organization, and perhaps its leadership.
The “soft” side of the inspection process is looking around at the people going about their work. Does the workflow appear to be reasonable, stable, and organized? Do workers appear to be fatigued, distracted, or unaware of what is going on around them? The next injury may come from someone making a poor decision due to fatigue rather than from an aisle being an inch too narrow or a missing fire extinguisher tag.
Many years ago, I was a safety director at a manufacturing facility. During a scheduled safety inspection with our loss control representative, we observed workers using considerable effort to move a cart loaded with product. A quick conversation with the workers revealed it was a constant frustration and nobody wanted to be assigned to the task. One of the employees made a seemingly innocuous comment: “You should try larger wheels.” A quick check with engineering revealed we could try fitting a set of larger wheels to a cart for testing. The force required to move the cart was reduced by 30%. This reduced the odds of an ergonomic injury, improved morale, and the safety director was popular…. for a while anyway.
Just communicating with the workers as you “inspect” can often reveal comments or concerns raised by employees. They may express concerns regarding their equipment, process, and procedures. Often you can find out about problems before someone gets hurt, giving you the opportunity for corrective action proactively rather than reactively. People may even express personal concerns about themselves or other employees. This can be a valuable tool to address issues surrounding “presenteeism” when people are at work but not fully engaged. This may be at the heart of many unsafe behaviors and resulting incidents. It gives you the opportunity to make corrective action, or get a person to the right resource, with positive results for everyone.
Communication is an essential part of the inspection process. In my opinion, one of the most important aspects is conveying to the employees your genuine concern for their safety and well-being. Don’t just be that person with the clipboard, checklist, and a pen. Use the time on the jobsite to observe, communicate, and elicit feedback from the people doing the job. You will be very surprised at the valuable information you receive about people, processes, and general goings on. You might find it even eases the tedium of the inspection process. Just remember, the soft science part of injury prevention might actually be the really hard part. It does take a lot of energy, commitment, and compassion for your fellow workers. But the results could be extremely rewarding.