Safety Programs: Are Yours Working?
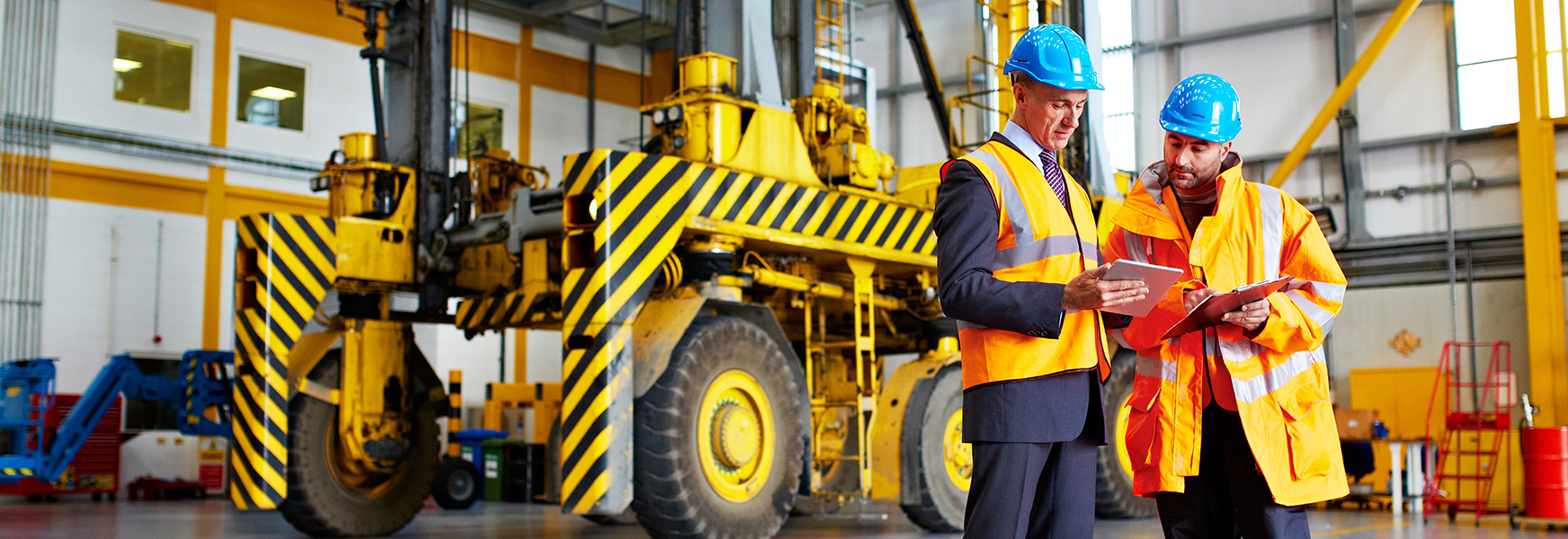
Safety programs are important for any business. After all, what is more important than taking care of the people who work for your organization? But often these programs seem so intimidating that very little is done to develop effective programs and even less to implement them with policies and procedures. It can seem daunting, even overwhelming. OSHA, EPA, DOT, NFPA, and many other alphabetic acronyms require a multitude of written programs. Where does one start? Well, Mark Twain once said, “The secret of getting ahead is getting started.” So do just that.
Large organizations likely have many written programs and have many hazard controls in place. High hazard industries will likely have set protocols and/or heavy governmental oversight to guide them. But what about the average small business? Sometimes just asking a few simple questions will guide you to the right starting point. For example:
- Do workers operate hazardous tools or equipment?
- Are workers exposed to harmful chemicals?
- Do workers drive vehicles for business?
- Are employees operating computers for hours each day?
- Are employees engaged in manual material handling?
If you answered “yes” to any of these questions, and most employers would, then a written program is likely required and standard controls are certainly required. The latter is easier to implement when the former is already in place. A written program should not be created just because OSHA says it should be. Programs should be helpful tools to ensure proper steps are taken to protect workers on the job.
Often conducting a Job Hazard Analysis (JHA) can help raise awareness and provide information that should be included in a training program. A JHA is used to identify tasks, the hazards associated with those tasks, and what controls are needed to reduce the likelihood of an injury. That information can be used to build a training program; a step by step guide for workers. It can include a sign-off page or other form of documentation as well as recurrent training requirements or refresher training. For more information on JHAs check out the OSHA publication 3071 entitled “Job Hazard Analysis.”
Safety Committees can also be a great resource to determine what formal programs are required. Committee members are selected from the workforce, so they know the jobs and the hazards. Who better to determine the required safety measures? These workers might have actually read the operator’s manual and really understand how to operate equipment safely. Use that resource!
There is no need to reinvent the wheel; templates are available from many sources. Sample program requirements and templates are available from OSHA and MEMIC policyholders can access many templates from the Safety Director.
Lastly, the real challenge is to make the written program into an effective injury prevention tool. A written program is the first step, but if it sits on a shelf in the office and is never read then obviously it serves no real purpose. Front-line supervisors are a key to this effectiveness. They must be dedicated to “doing the right thing” every day. Programs are valuable only if they are:
- Relevant and updated regularly.
- Implemented in the workplace consistently.
- Read and understood by all affected employees.
- Used to hold everyone accountable for the program requirements.
A large business may have dozens of written programs. A small business might need only a few. But if workers are unaware of the rules or they are not required to follow the rules then the inevitable injuries will occur. Safety is not rocket science, but it does require attention and adherence to policy. These programs are written in blood, so do everyone a favor and require universal compliance. The injury you prevent could be a life saver- literally. Mark Twain also said, “Do the right thing. It will gratify some people and astonish the rest”.
By Randy Klatt