Low Frequency Doesn't Always Mean Low Risk
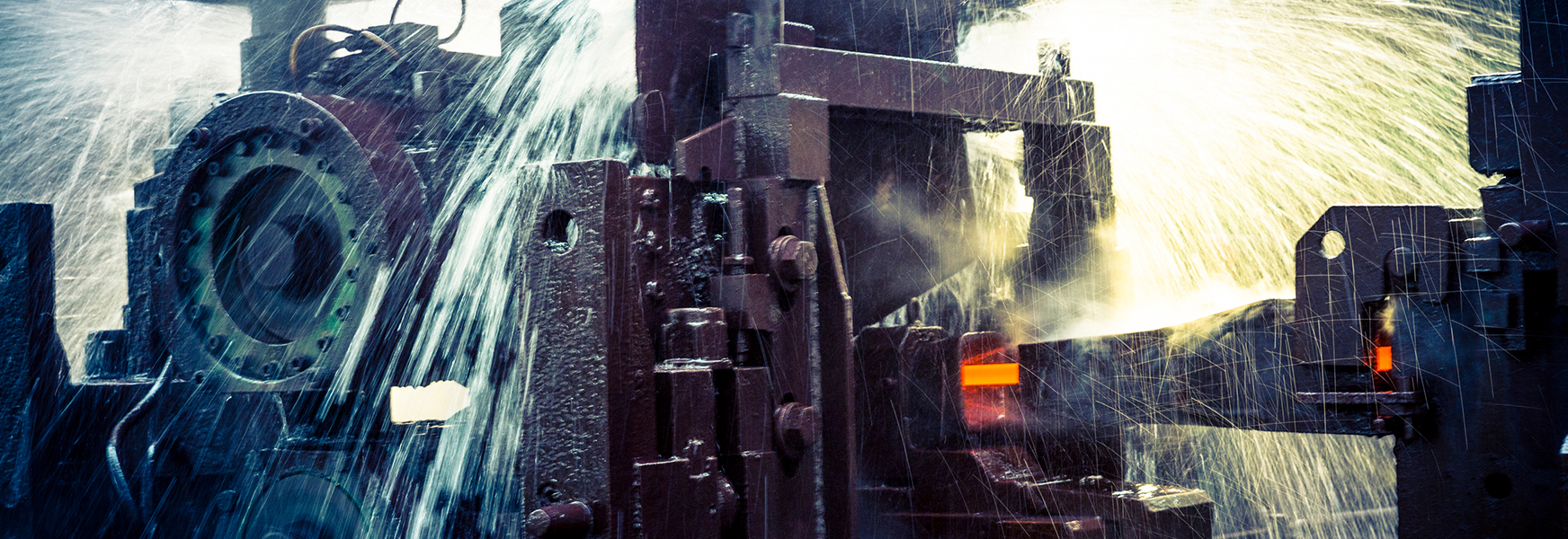
Watch your toes! Manufacturing safety programs are often built around injury trending. The potential problem with this approach is that low-frequency activities could be overlooked because they don’t provide enough data to generate a trend. Certain activities in a facility may be of equal or higher risk than those that occur during regular production, but they happen so infrequently that the risk isn’t recognized.
Take for instance, the steel fabrication business. What first comes to mind is heavy steel falling on unprotected toes, fingers amputated by shears, and hands crushed by press-brakes. Employees are well aware of these risks and take measures to mitigate them during normal operations. What they may not address are the hazards related to the adjustment, securement, or repair of the equipment they work with regularly.
I have a good friend, let’s call him Joe, who owns a sizable steel fabrication shop. There are three press-brakes in the shop ranging in capacity from 50 to 200 tons. All three of them have lower dies that can be rotated to one of four positions, depending on the desired bend radius. Some time ago, he was using the 50-ton press-brake and needed to change the position of the lower die. At the time, there was a chain hanging from each end of the upper die that simply slid over a corresponding headless pin on the lower die. He lowered the upper die, slipped the chains over pins on the lower die, and began to lift the lower die so he could spin it to the right position.
Unfortunately, the die spun by itself when lifted and slipped out of the lift chain on the far side. As the far end hit the floor it came out of the near lift chain and fell 42” onto Joe’s foot. The resulting trauma resulted in the need for reconstructive surgery and over a year of physical therapy.
With a number of other employees in his shop, Joe made it an immediate priority to prevent another similar incident. On all three brakes the lift chains were relocated and secured to the lower die with bolts or pins. On two of them grab hooks were added (Images 1 and 3), and on the other a bracket was modified to allow for the chain to be looped over it (Image 2).
In this configuration, the lift chains are positively engaged with the upper sector the second they are put to use. This also allows for them to hang out of the way when not in use.
1. Chain formerly hung from the top with no head on lower pin
|
2. Bolted chain loop with lifting bracket |
![]() |
![]() |
3. Bolted chain with hook on upper die | 4. 200 ton brake |
![]() |
![]() |
It’s unfortunate that a serious injury occurred before Joe became fully aware of the dangers of rotating the lower die. Conducting a Job Safety Analysis (JSA) prior to conducting this task could have identified the hazards. The corrective action could have taken place before the injury instead of after. Furthermore, completing a JSA with input from an employee more familiar with the equipment might have provided invaluable input from a different perspective. Take a look around your facility and identify the low frequency-high risk activities that may occur. Then take steps to ensure that a JSA is performed before initiating them. The toes you save could be yours!
For more information regarding press-brake safety check out the OSHA Machine Guarding eTool, this resource from Harvard EHS, or log into the Safety Director at MEMIC.com.
By Barrett Parks