Human Error
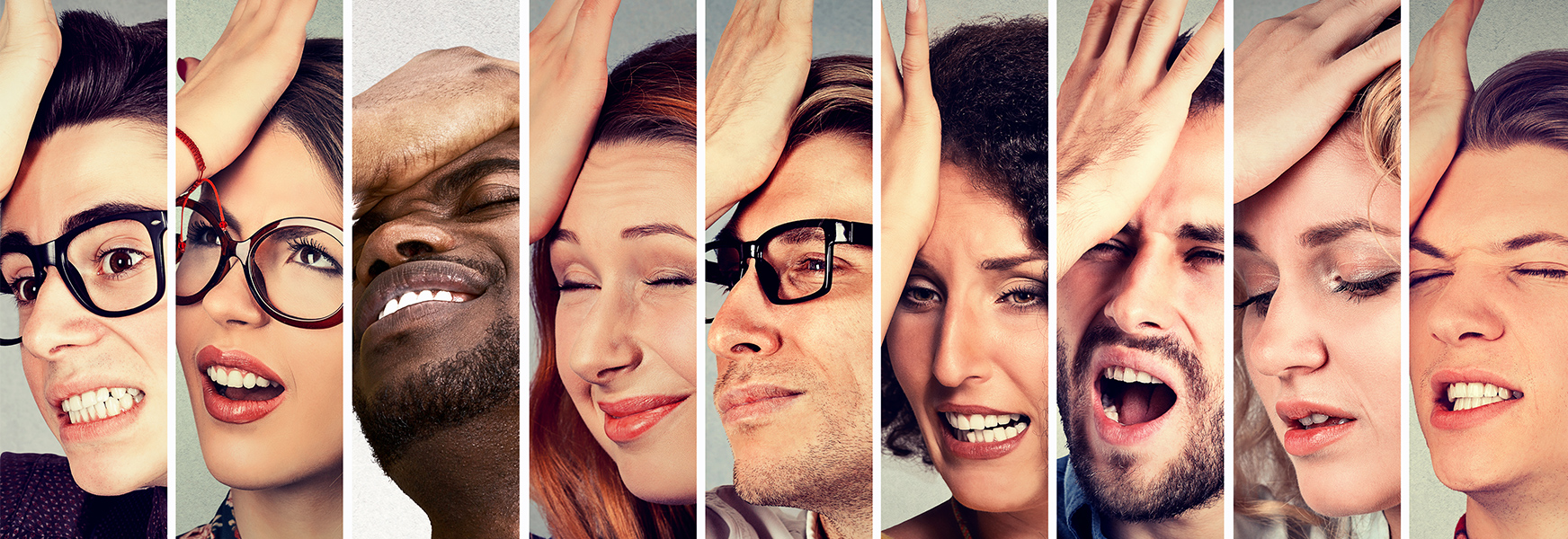
I recently scheduled an appointment with a policyholder in Boston, one that I had visited several times. I left plenty of time to deal with traffic and walked through the door right on time – only to discover I was at the wrong policyholder! How could I have made such a stupid mistake? Well, I seemed to be operating on “autopilot.” Merriam-Webster defines “autopilot” as “a state or condition in which activity or behavior is regulated automatically in a predetermined or instinctive manner.” Sounds exactly like what I was doing. While this example only led to my embarrassment and minimal delay, these types of human error can often have implications for safety.
Human error, or human failure, can be categorized in several ways. Consider the following types of human errors:
- Slips – Not doing what you intended to do. These are the “Whoops!” errors like my example of performing the driving task safely, but ending up at the wrong destination.
- Lapses – Forgetting to do something like putting on a seat-belt, or closing a door.
- Mistakes – Decision-making failures. Selecting the wrong item from a pull-down menu for example.
- Violations – Deliberate errors, or intentional failures such as not following procedures when under time pressures.
Let’s take a closer look at slips and what can be done at your workplace to prevent them. Slips occur when tasks are familiar or routine. The task takes little thought and/or is similar to other tasks. There may be interruptions during the task. Boredom or complacency can rear their ugly heads in these cases.
Adding more training will not prevent slips! But there are proven ways to reduce slips. Effective procedures are needed to reduce the likelihood of slip errors.
- Use checklists to help guide actions and confirm completion. This is the most effective method for preventing slip-type errors. If followed, checklists ensure all steps are performed in the correct sequence. A 2007 study showed that surgical checklists dramatically improved safety outcomes.
- Set-up worksites to ensure there is a logical sequence for task completion. Laying out the proper tools in advance may prevent someone from slipping up and grabbing the wrong tool.
- Minimize distractions and interruptions. For example, establish a mobile phone policy on the worksite.
- Fatigue can be a factor. Well-rested, hydrated, and alert employees are one obvious solution. Employing task rotation; switching between tasks or alternating tasks can be an effective way to combat task fatigue such as boredom or daydreaming on the job.
While training won’t prevent slips, raising awareness will help. “Morning Huddles” or daily staff meetings are great places to raise awareness of slip errors. Remind employees about checklists or routines. To further raise awareness use “near-miss” incidents that involved slip-type errors as discussion points.
From highly-trained medical personnel to entry-level laborers, all employees are vulnerable to slip-type errors. After all, we are all human. Employers should have policies and procedures in place to minimize the risk of slip-type errors. MEMIC policyholders can access the Safety Director for more information, templates, sample plans, and training ideas for all industries.
In my own work, I will double-check my appointment calendar to ensure I am going to the correct location!
By Maureen Anderson